Приход теплоты
= + + + 
Приход энергии происходит за счет статей:
где – электроэнергия, необходимая для нагрева, расплавления и перегрева металлического лома, кДж;
– физическая теплота материалов, поступающих в печь, кДж;
– суммарное количество теплоты от сгорания природного газа, кДж;
– теплота от экзотермических реакций, кДж.
1. на действующей печи определяется по показаниям счетчика активной энергии, установленного на печи, а по показаниям счетчика реактивной мощности определяется средний коэффициент мощности установки (cos j). Эта статья для печей одной емкости составляет 60 – 80 %.
= 179460000 кДж
2. - суммарное количество теплоты от горелок (стеновые газокислородные горелки и комбинированные рафинирующие горелки)
= Ʃ ˖ , кДж,
где Ʃ - объем природного газа, расходуемый на всю плавку, ;
- низшая теплота сгорания природного газа, кДж/ ;
868*35392=30720256 кДж
3. физическая теплота материалов, поступающих в печь.
= , где
, – масса загружаемого лома, извести и кокса, кг;
, , – истинные теплоемкости лома, извести и кокса, кДж/(кг*°С);
, , – температура материалов, °С;

4. приход теплоты от экзотермических реакций.
,
- количество теплоты, которое выделяется в результате окисления углерода кокса и электродов, кДж
- количество теплоты, которое выделяется в результате окисления серы, кДж
- количество теплоты, которое выделяется в результате окисления алюминия, кДж
- количество теплоты, которое выделяется в результате угара железа, кДж
- количество теплоты, которое выделяется в результате окисления фосфора, кДж
- количество теплоты, которое выделяется в результате окисления кремния, кДж
- количество теплоты, которое выделяется в результате окисления марганца, кДж
Окисление углерода
Окисление углерода происходит по реакции:
С+ = + ,
где = * Ʃ , – тепловой эффект окисления углерода, кДж/кг;
Ʃ – масса окисленного углерода, кг.
Исходя из баланса времени и плавки, время работы электродов составляет 65%, а удельный расход электродов за плавку – 1, 65кг/т, тогда за период плавления расход электродов составляет:
=1, 65*0, 65=1, 073 кг/т
Общее количество выгоревшего углерода из электродов:
=1, 073*129, 7=139, 2 кг
В печь поступает кокс массой 1685 кг. Учитывая состав кокса, определим массу углерода:
=1685*0, 96=1617, 6кг
По данным паспорта плавки определим содержание углерода в ломе (0, 086%) и в полупродукте (0, 329).
=(0, 086*129700)/100=111, 5 кг,
=(0, 329*129700)/100=426, 7кг.
Следовательно, недостающую часть углерода в полупродукте вычислим по формуле:
= 426, 7-111, 5=315, 2 кг
Количество окислившегося углерода до СО вычислим по формуле:
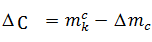

Т.е. из всего углерода кокса, подаваемого в печь, окисляется:
(1302, 4/1617, 6)*100=80, 91%
Суммарное количество окислившегося углерода составляет:
Ʃ = , кг
Ʃ =1302, 4+139, 2=1163, 2 кг
Количество теплоты от окисления углерода кокса составит:
=34100*1163, 2=39665120 кДж
Окисление серы
Окисление серы происходит по реакции:
S+ = + ,
где = * Ʃ ,
где – тепловой эффект окисления серы, кДж/кг;
Ʃ – масса окисленной серы, кг.
По данным паспорта плавки вычислим массовое количество серы в скрапе:
=(0, 048*129700/100)=62, 3 кг,
В полупродукте количество серы составляет:
=(0, 022*129700)/100=28, 5 кг.
Предполагаем, что масса окислившейся серы будет:
=62, 3-28, 5=33, 8 кг.
Количество теплоты от окисления серы определим по формуле:

Окисление алюминия
Окисление алюминия происходит по реакции:
4/3Al+ = + ,
где = * , – тепловой эффект окисления алюминия, кДж/кг;
– масса окисленного углерода, кг.
По данным паспорта плавки количество алюминия составляет:
=(0, 909*129700)/100=1179 кг
В процессе плавки весь алюминий окисляется, значит, количество теплоты от окисления алюминия определим по формуле:
=28600*1179=33719400 кДж.
Окисление железа
Угар железа в ванне за период плавки составляет 142 кг/т.
Тогда общее количество железа, окислившееся до FeO и , составит:

Принимаем, что железо окисляется до FeO и в соотношении 50/50. Значит .
Окисление железа до FeO происходит по реакции:
2Fe+ =2FeO+ ,
где = * , – тепловой эффект окисления железа до FeO, кДж/кг;
– масса угара Fe при окислении до FeO, кг.
=4820*9208, 7=44385934 кДж
Окисление железа до происходит по реакции:
4/3Fe+ = + ,
где = * , – тепловой эффект окисления железа до , кДж/кг;
– масса угара Fe при окислении до FeO, кг.
=7300*9208, 7=67223510 кДж
=67223510+44385934=111609444 кДж
Окисление фосфора
Окисление фосфора происходит по реакции:
4Р+ = + ,
где = * Ʃ , – тепловой эффект окисления фосфора, кДж/кг;
Ʃ – масса окисленного фосфора, кг.

Окисление кремния
Окисление кремния происходит по реакции:
2Si+ =2Si + ,
где = * Ʃ , – тепловой эффект окисления кремния, кДж/кг;
Ʃ – масса окисленного кремния, кг.
Так как содержание кремния в ходе плавки не менялось, тогда 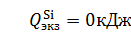
Окисление марганца
Окисление марганца происходит по реакции:
2Мn+ =2Mn + ,
где = * Ʃ , – тепловой эффект окисления марганца, кДж/кг;
Ʃ – масса окисленного кремния, кг.
Так как содержание марганца в ходе плавки не менялась, тогда =0кДж
Расход теплоты
= + + + + ,
где – расход теплоты для нагрева, расплавления и перегрева металла до заданной температуры, кДж;
– потери теплоты с отходящими газами, кДж;
– потери теплоты с химическим недожогом, кДж;
- потери теплоты с уносимой коксовой пылью, кДж. Данные потери малы и поэтому принимаем их за ноль.
– потери теплоты в окружающую среду:
– потери теплоты теплопроводностью через под печи, кДж;
– потери теплоты теплопроводностью через поверхность не водоохлождаемой части стенки печи, кДж;
– потери теплоты излучением через открытое рабочее окно, кДж;
– потери теплоты излучением из рабочего пространства печи во время подвалки шихты, кДж;
– потери теплоты от внутренней поверхности свода во время подвалки шихты, кДж;
– потери теплоты с охлаждающей водой, кДж;
1. расход теплоты для нагрева, расплавления и перегрева металла до заданной температуры.
= , кДж,
- теплота, затраченная на нагрев, расплавление и перегрев скрапа, кДж
– теплота, затраченная на нагрев шлака, кДж
= * , кДж,
– удельная теплота расходуемая на нагрев, плавление и перегрев скрапа до заданной температуры, кДж
– масса скрапа, кг
= , кДж, где
– средние теплоемкости твердого и жидкого металла, кДж/(кг*°С);
, – температуры плавления и перегрева металла, °С;
– средняя теплота плавления, кДж/кг
=0, 348*(1550-20)+268+0, 46*(1650-1550)=846 кДж/кг
=846, 44*129700=109783268 кДж
Теплоту, затраченную на нагрев шлака, определим по формуле:
= , кДж,
где – количество шлака перед его спуском, кг;
– средняя теплоемкость шлака, кДж/(кг*°С);
– температура шлака, °С;
Общее количество шлака, перед его спуском, для принятой шихты составит 9, 6% от массы металла, т.е. =0, 096*129700=12451, 2 кг
=12451, 2*0, 17*1670=3492561, 6 кДж.
Тогда расход теплоты на нагрев, расплавления и перегрев металла до заданной температуры будет составлять:
=109783268+3492561, 6=113275830 кДж.
2. Потери теплоты с отходящими газами.
= ,
где – объем отходящих газов за период плавления металла, ;
средняя теплоемкость отходящих газов, кДж/ ;
, - температура газов в период плавления, °С;
=Ʃ ,
где Ʃ – общий объем отходящих газов, 
– период плавления металла, ч;
=120000*0, 72=86400 
кДж/ ,
где , , – средние теплоемкости газов при , кДж/ ;
, – концентрации компонентов в отходящих газах, %;
Объем воды в дымовых газах будет равен:
=1, 98 
=1, 98*868=1720.4 
0, 01*(2, 1692*10+1, 3996*20+0, 998*1, 4+1, 4645*15+1, 3846*53, 6) =1, 47 кДж/ ,
= ;
=(1800-20)/2=890°С
=86400*1, 47*890=113037120 кДж
3. Потери теплоты с химическим недожогом.
* * кДж,
где - объем отходящих газов за период плавления металла, ;
– концентрация оксида углерода в отходящих газах, %;
- теплота сгорания оксида углерода, кДж/ ;
=0, 01*86400*10*12644=109244160 кДж
4. Потери теплоты в окружающую среду .
4.1. Потери теплоты теплопроводностью через под печи.
= кДж,
где – удельный тепловой поток, кДж/ ;
– площадь наружной поверхности пода, ;
= (( / ,
– температура внутренней поверхности стенки и окружающей среды, °С;
толщина i-того слоя, м;
– теплопроводность материала i-того слоя, / °С);
– суммарный коэффициент теплоотдачи от внутренней поверхности в окружающую среду, Вт/( °С);
– время плавления металла, с;
Подина состоит из 4-х слоев:
· металлический каркас печи толщиной 0, 035 м. Коэффициент теплопроводности составляет =48, 1 Вт/( °С);
· асбестовый картон толщиной 0, 015м. Коэффициент теплопроводности асбестового картона вычислим по формуле:
=0, 16+0, 14* *t, Вт/( °С);
=0, 16+0, 14* *500=0, 23, Вт/( °С).
· Кирпичная кладка в 2 ряда толщиной 0, 075 м.
Таблица 4. – Физико–химические свойства периклазового материала.
Материал
| Содержание, %
| Плотность,
кг/
| Пористость,
%
| MgO
| CaO
| Si
|
| П - 2
| более 91
| менее
| менее
| менее 2, 5
| более
| менее
| Коэффициент теплопроводности периклазового материала вычислим по формуле:
=6, 84-6, 1* *t+2, 2* =2, 93, Вт/( °С);
=6, 84-6, 1* *1000+2, 2* =2, 93, Вт/( °С).
· Для рабочего слоя футеровки подины применяют периклазовые или периклазуглеродистые набивные массы толщиной 0, 5 м.
Таблица 5 – Физико химические свойства масс рабочего слоя подины
Материал
| Содержание, %
| Температура эксплуатации,
°С
| Флакция,
мм
| MgO
| CaO
| Si
|
| Набивная масса
| 75-77
| 8-20
| 0, 6
| 0, 4
| более
| 0-5
|
Коэффициент теплопроводности набивной массы вычислим по формуле:
=12, 2-11, 7* *t+4, 4* =2, 93, Вт/( °С);
=12, 2-11, 7* *1650+4, 4* =4, 87, Вт/( °С)
Коэффициент теплоотдачи от наружной поверхности в окружающую среду рассчитывается по формуле:
=К* Вт/( °С),
где К – коэффициент, учитывающий положение горизонтальной поверхности в пространстве;
-температура окружающей среды и наружной поверхности пода, °С;
- температура окружающей среды и наружной поверхности пода, К;
– постоянная Стефана-Больцмана, Вт/( ;
– степень черноты наружной поверхности стенки пода;
=1, 6* Вт/( °С);
=(1650-20)*3324/(0, 015/0, 23+0, 035/48, 1+0, 15/2, 94+0, 5/4, 87+1/14) =18693, 3 / ;
Поверхность пода при сферическом днище с точностью, достаточной для инженерного расчета, примем ровной и рассчитаем по формуле:
, 
1.15*3.14* =41, 7 
Потери теплопроводностью через под печи:

4.2. Потери теплоты теплопроводностью через поверхность не водоохлождаемой части стенки печи.
= кДж,
где – удельный тепловой поток, кДж/ ;
– площадь наружной поверхности не водоохлождаемой стенки, ;
=2.4* Вт/( °С);
=(1650-20)*3324/(0, 015/0, 23+0, 035/48, 1+0, 46/4, 87+1/16, 7) =24627, 8 / ;
Площадь поверхности стенки
= * , ,
- внутренний диаметр кожуха, м;
- футерованная высота стенок, м;
=3, 14*6, 8*0, 9=19, 2 
=24627, 8*19, 2=472853, 76 кДж.
.3. Потери теплоты через открытое рабочее окно.
Потери теплоты излучением вычисляют по следующей формуле:
= кДж,
где – удельный тепловой поток, кДж/ ;
– площадь наружной поверхности не водоохлождаемой стенки, ;
Ф – коэффициент диафрагмирования.
= ,
– приведенный коэффициент излучения, кДж/( ;
, - температура в печи и окружающей среды, К;
– период времени открытого рабочего окна, ч;
=16, 7 кДж/ ;
Площадь рабочего окна:
,
Где а – ширина рабочего окна, м;
b – высота рабочего окна, м;
=1, 3*0, 99=1, 29 
=91297, 6*1, 29*0, 65=76553 кДж
4.4. Потери теплоты излучением из рабочего пространства печи во время подвалки шихты.
= кДж,
– удельный тепловой поток, кДж/( ;
– площадь рабочего пространства печи, ;
– период времени открытого рабочего пространства печи, ч;
=16, 7 кДж/ 

= * , ,
– внутренний диаметр свода печи, м;
= (3, 14 * )/4=40 ,
=1959157*40*0, 034=2664454 кДж
4.5. Для определения потерь теплоты от внутренней поверхности свода во время подвалки шихты.
= кДж,
– плотность теплового потока, кДж/( ;
– площадь внутренней поверхности свода, ;
– период времени подвалки шихты, ч;
=16, 7 кДж/ 

= * , ,
= (3, 14 * )/4=41, 5 
=1959157*41, 5*0, 034=2764371 кДж
4.6. Потери теплоты с охлаждающей водой.
= кДж,
– потери теплоты с охлаждающей водой на своде, кДж;
- потери теплоты с охлаждающей водой на кожухе печи, кДж;
кДж,
– объем воды, расходуемый на охлаждение свода, кг/ч;
– теплоемкость воды при температур , кДж/(кг*°С);
– разность температур воды навыходе и входе водоохлаждаемого элемента, С;
– время плавки, ч;
=475000*4, 2013*15*0, 92=27539521, 5 кДж
кДж,
– объем воды, расходуемый на охлаждение кожуха печи, кг/ч;
– теплоемкость воды при температур , кДж/(кг*°С);
– разность температур воды навыходе и входе водоохлаждаемого элемента, С;
– время плавки, ч;
=875000*4, 2058*10*0, 92=33856690 кДж
Суммарные потери с охлаждающей водой:
=27539521, 5+33856690=61396211, 5кДж
Общие потери теплоты в окружающую среду:
= + + + + + 
= 472853, 76+76553+2664454+2764371+61396211, 5 =68154760 кДж
=113275830+113037120+109244160+68154760= 403711870 кДж
=(403711870-396867014)*100/403711870=1, 7%
Таблица 6. – Сводные данные о тепловом балансе печи.
Параметр
| кДж
| %
| Приход теплоты
| 1.Приход теплоты от электрической дуги
|
| 45, 2
| 2.Теплота от сгорания природного газа
|
| 7, 7
| 3.Физическая теплота материалов:
Металлического лома
Извести
Кокса
| 1381291, 4
86874, 4
| 0, 35
0, 31
0, 02
0, 015
| 4.Приход теплоты от экзотермических реакций:
Окисления углерода
Окисления алюминия
Окисления серы
Угара железа
|
311500, 8
| 46, 7
8, 5
0, 08
28, 1
| Суммарный приход теплоты
|
|
| Расход теплоты
| 1.Расход теплоты на нагрев и расплавление шихты, перегрев металла.
|
| 28, 05
| 2.Потери теплоты с отходящими газами
|
|
| 3.Потери теплоты с химическим недожогом
|
| 27, 05
| 4.Потери теплоты в окружающую среду:
· Потери теплоты теплопроводностью через под печи
· Потери теплоты теплопроводностью через поверхность не водоохлождаемой части стенки печи
· Потери теплоты через открытое рабочее окно
· Потери теплоты излучением из рабочего пространства печи во время подвалки шихты
· Потери теплоты от внутренней поверхности свода во время подвалки шихты.
· Потери теплоты с охлаждающей водой
|
472853, 76
61396211, 5
| 16, 9
0, 19
0, 12
0, 02
0, 66
0, 68
15, 2
| Суммарный расход теплоты
|
|
|
Заключение
В ходе данного курсового проекта были рассчитаны горение природного газа в кислороде и воздухе, материальный и тепловой баланс дуговой сталеплавильной печи ёмкостью 120 тонн (ДСП - 120) фирмы «Даниэли».
Преимущества электроплавки по сравнению с другими способами сталеплавильного производства связаны с использованием для нагрева металла электрической энергии. Выделение тепла в электропечах происходит либо в нагреваемом металле, либо в непосредственной близи от его поверхности. Это позволяет в сравнительно небольшом объеме сконцентрировать значительную мощность и нагревать металл с большой скоростью до высоких температур, вводить в печь большие количества легирующих добавок; иметь в печи восстановительную атмосферу и безокислительные шлаки, что предполагает малый угар легирующих элементов; плавно и точно регулировать температуру металла; более полно, чем других печах раскислять металл, получая его с низким содержанием неметаллических включений; получать сталь с низким содержанием серы. Расход тепла и изменение температуры металла при электроплавке относительно легко поддаются контролю и регулированию, что очень важно при автоматизации производства.
Электропечь лучше других приспособлена для переработки металлического лома. В электропечах можно выплавлять сталь обширного сортамента.
Список литературы
· Скрап карбюраторный процесс при производстве стали в мартеновских печах./В.А.Старцев, Г.В.Воронов, В.И.Лобанов, Э.А.Шумахер, Э.Э.Шумахер. Екатеринбург 2004г.
· Дипломное и курсовое проектирование теплотехнических агрегатов/ Н.Б. Лошкарев, А.Н. Лошкарев, Л.А. Зайнулин. Екатеринбург: ГАО ВПО УГТУ – УПИ, 2007.
· https://uas.su/books/2011/kslitok/12/razdel12.php
· Григорьев В.П., Нечкин Ю.М., Егоров А.В., Никольский Л.Е./ Конструкции и проектирование агрегатов сталеплавильного производства. М. изд. «Металлургия». 1995г.
· Паспорт плавки № 722734 от 11.05.2007.
· Кацевич Л.С. «Расчет и конструирование электрических печей.»,
М.: «Энергия», 1972г.
· Дорогов Н.И. «Тепловой и материальный балансы электро-
сталеплавильных печей.», М.: «Энергия», 1971г.
|